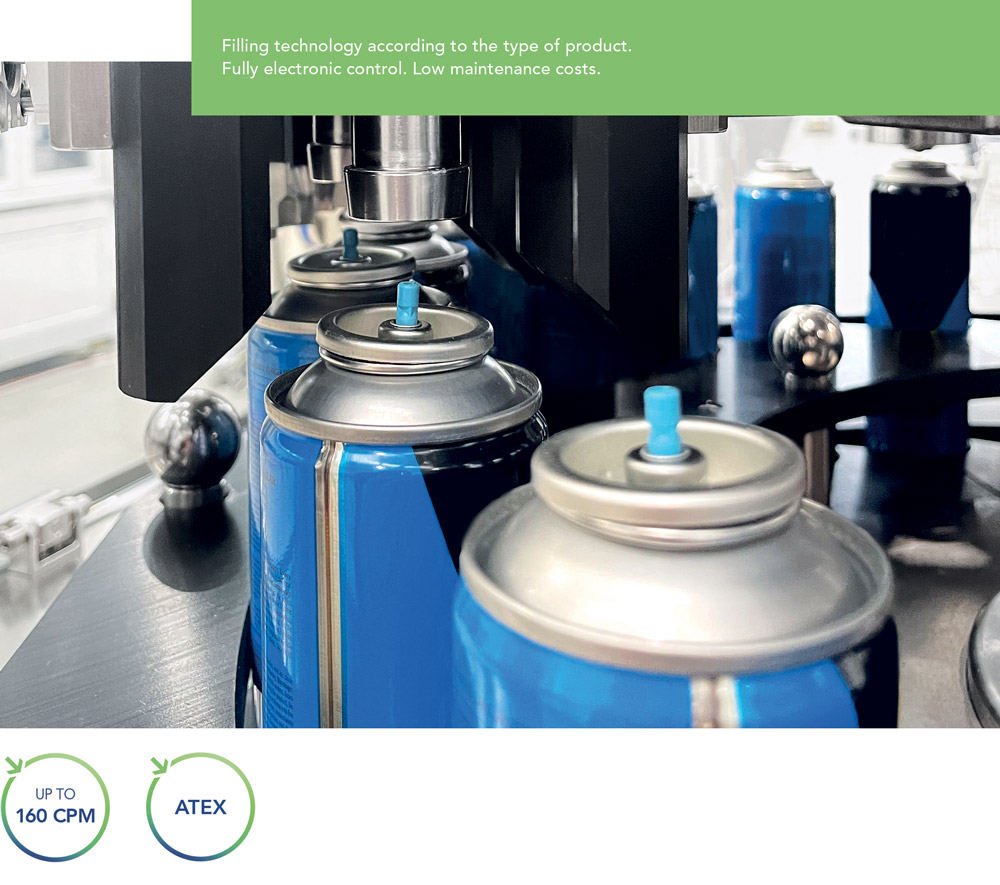
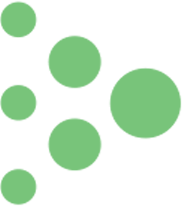
MR
PRODUCT FILLING AND CRIMPING
AUTOMATIC MULTIPLE INDEXING ROTARY MACHINE SUITABLE FOR FILLING WITH ALL TYPES OF AEROSOL PRODUCTS
MR machines are equipped with a servo-motor to drive a star-wheel up to 28 pockets.
In line layout can be configurated to fit Customer needs even in ATEX execution.
Different filling systems available:
↘ volumetric pumps
↘ flowmeter technology
Membrane filling heads for hygienic solutions are available on request. Universal feeding system suitable for all types of aerosol valves.
Crimping head with special material cartridge system that allows replacing even a single finger and guarantees long lasting use without lubrication.
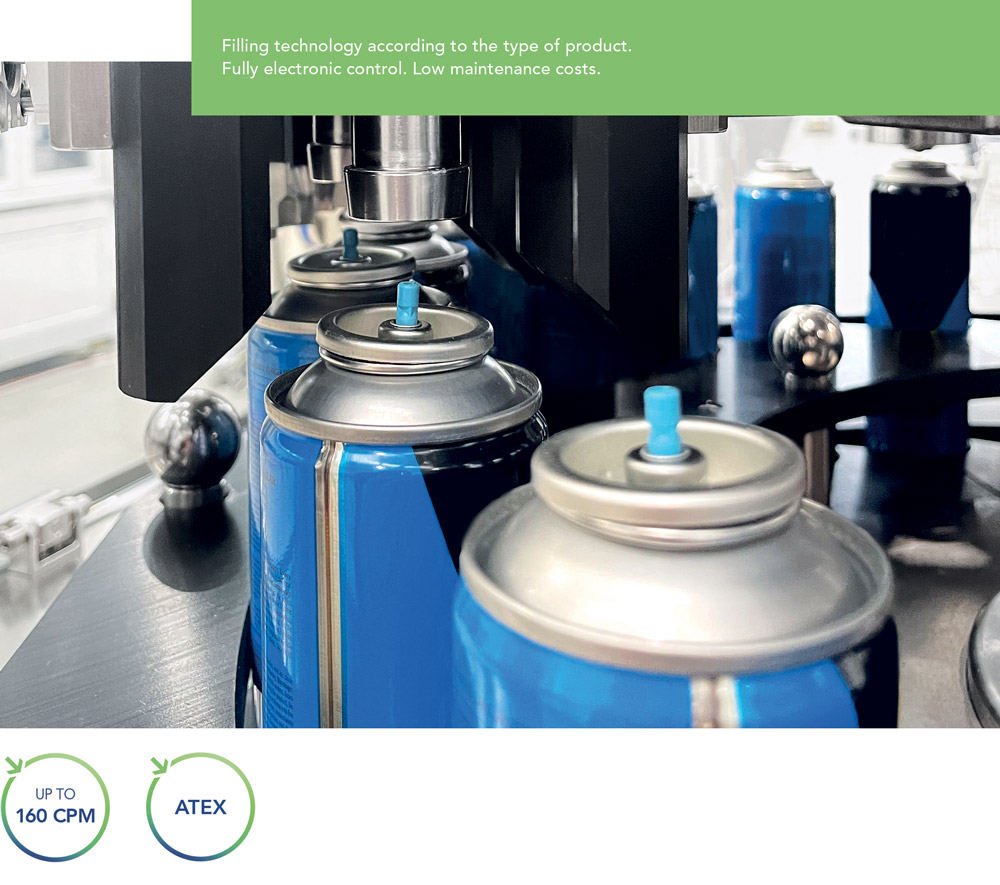
FEATURES
↘ Max speed up: 160 cpm
↘ Products: all type of liquid up to 10.000 cp
↘ Type of cans: tin plate and aluminium aerosol cans
• Diameter of cans: Ømin 35 mm – Ømax 66 mm
• Height: up to 320 mm
↘ Type of valves: 1” standard aerosol valves, aluminium and tin plate
↘ Standard voltage: 400V-50Hz
↘ Air working pressure: 6-8 bar
↘ Air consumption: 2500 Nl/min (depending on the configuration of the machine).
STANDARD CONFIGURATION
↘ Single and multiple indexing
↘ Product filling: up to 8 product units (no can-no fill)
(the capacity can be 100 ml, 300 ml or flowmeter system)
↘ Valve inserting: mechanical sorter with air blowing system, double tube placing and dip-tube centering funnel.
↘ Valve presence: pneumatic checking unit with PDS (Positive Displacing System) for dimpled valves
↘ Crimping of the aerosol valve unit.
TAILOR-MADE CONFIGURATION
↘ Ball insertion
↘ Vacuum
↘ CIP & SIP Units
↘ Inserting of valves without dip-tube.
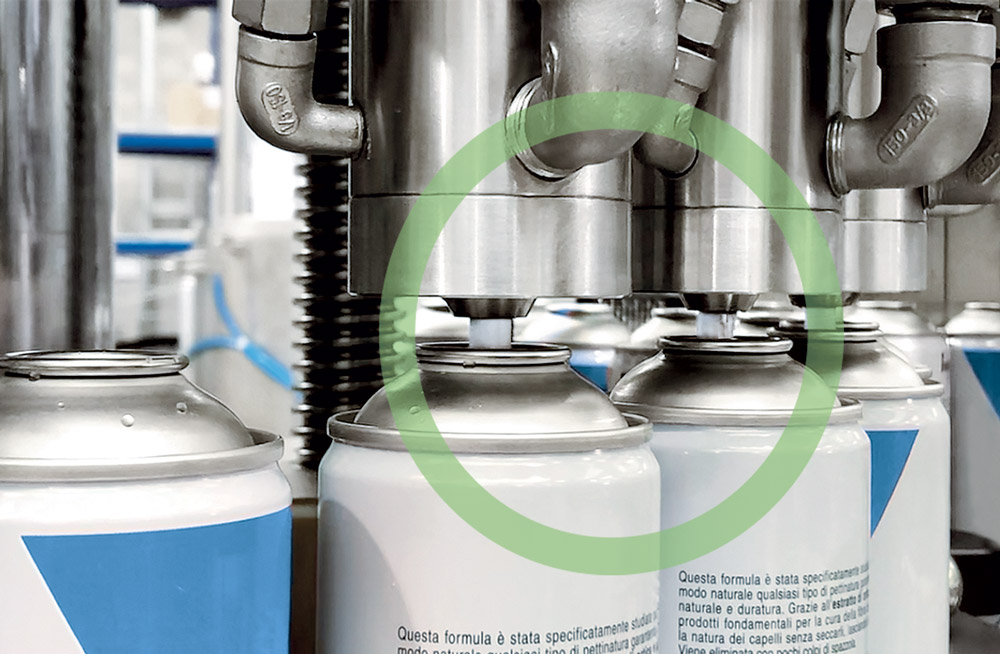
↘ 1 TO 2 DIVERTER CONVEYOR
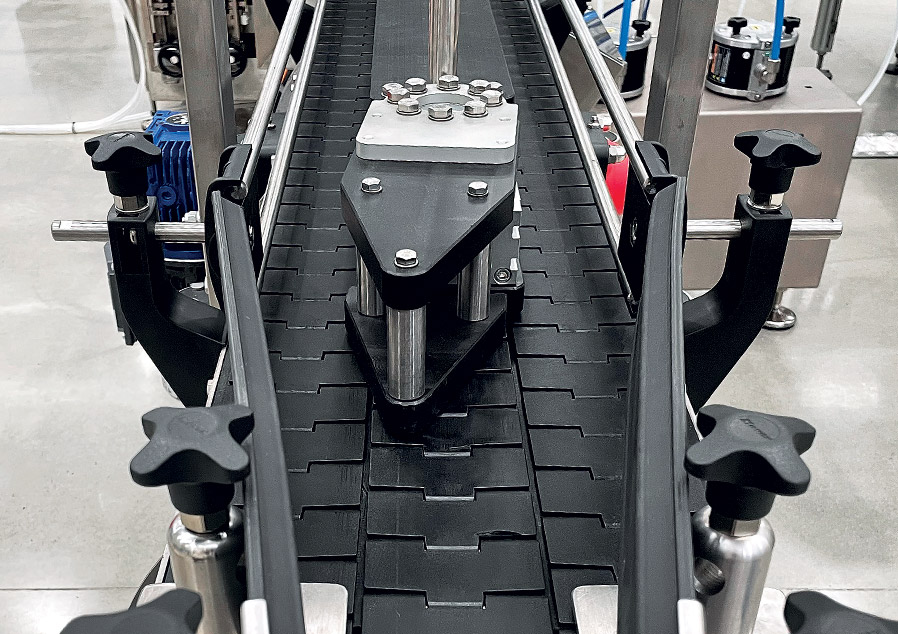
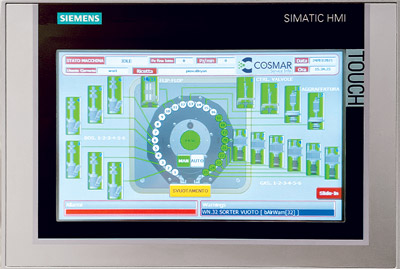
↖ HMI TOUCH DISPLAY
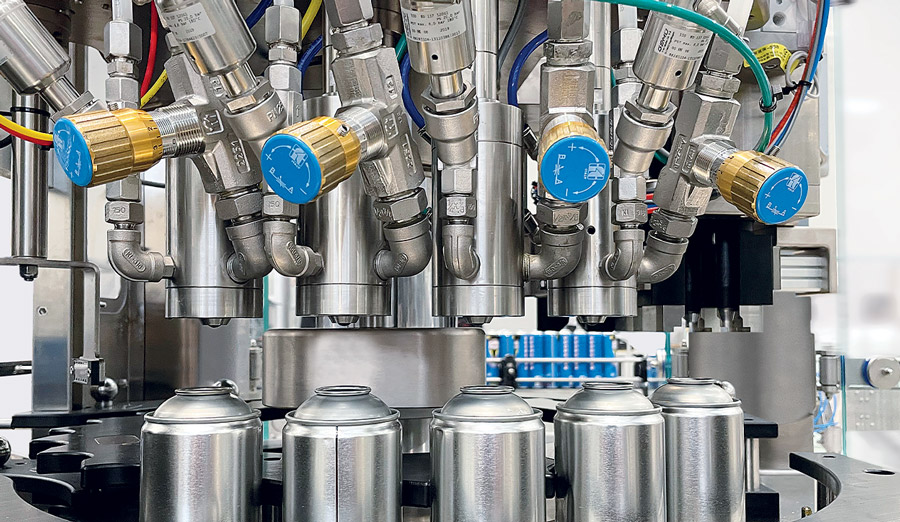
↗ FILLING HEADS WITH RECIRCULATION SYSTEM
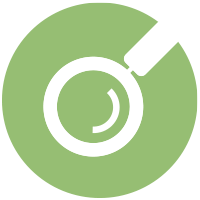
FLOWMETER TECHNOLOGY
The functionality of mass flowmeters is based on the Coriolis principle of controlled force generation. The liquid moves through two tubes which oscillate at their own resonant frequency.
Two electrodynamic sensors positioned at the entrance and exit of the two pipes, allow the detection and the displacements of the Coriolis effect.
Using the Coriolis force principle, the volume of the mass can be determined regardless of conductivity, density, viscosity and temperature of the liquids to be dosed.
This technology allows dosing all type of liquid with constant accuracy of the volume to be filled.
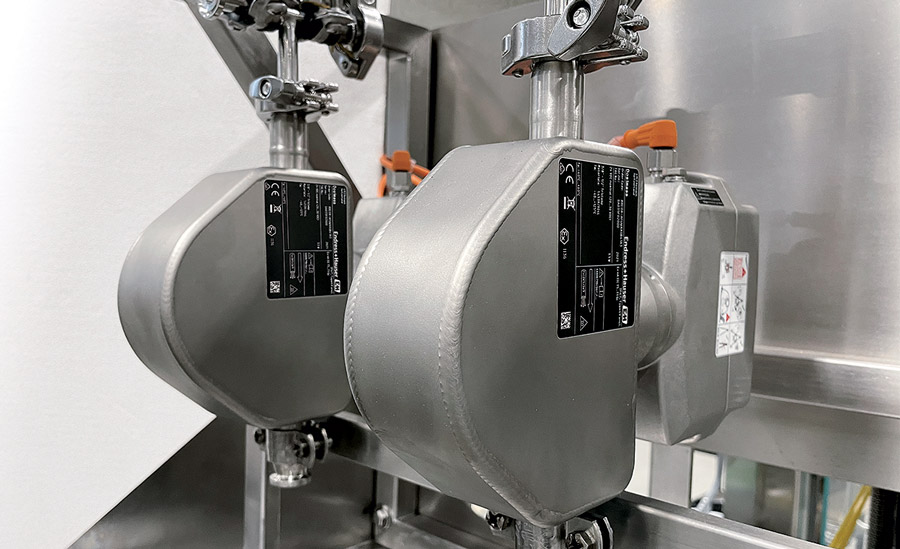
FLOWMETER SYSTEM
This kind of technology guarantees many advantages:
↘ Cleanability. The circuit is only a pipe from pump to the filling head.
↘ Accuracy. The filling accuracy does not depend on the volume to be filled and can be improved by fine tuning of the setup of the machine.
↘ No limit of the filling capacity. The filling volume can be setup as required, even for filling many liters.
↘ Reduced changeover time. The time for changing the product is reduced to few minutes and it doesn’t require any adjustment, just put the filling volume in the HMI and the system start to fill.
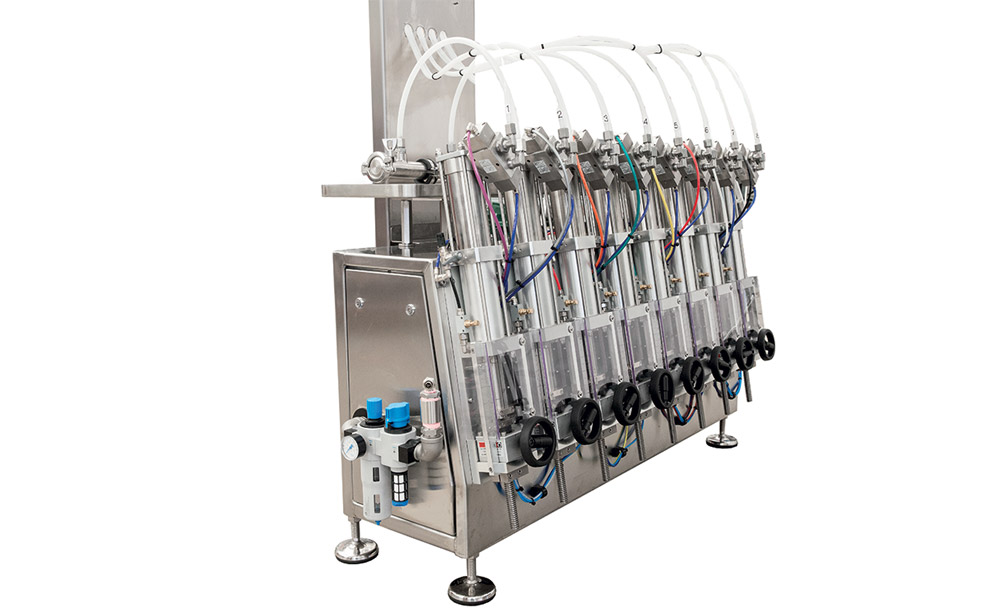
Volumetric doser
This technology is well consolidated and can be installed in all MR machines.
The liquid can be sucked from a side tank or a pump can transfer the product to the doser.
The dosing cylinders are installed next to the machine to allow easy access for quick volume adjustment, thanks to a handwheel and indicator.
The cylinders are long lasting and their special gaskets allow filling of several types of liquid.
MR Multitasking GMP Filling
↘ Saline solutions with 1” BOV
↘ Nasal sprays with snap-on pumps
↘ Throat sprays with Nitrogen and 20 mm crimp-on
valves
Each filling process is managed separately with dedicated operating stations.
The unit is fully electronic and the operator can decide the specific production on the HMI.
Features
All the materials in contact with product are FDA compliant and suitable for CIP/SIP process.
The machine can be equipped with COSMAR Air-Q system to create inside tthe guarding a LAF (Laminar Air Flow) for pharmaceutical filling.
The class that can be achieved is class ISO 5 or more.
↘ ACCURATE FILLING SYSTEM
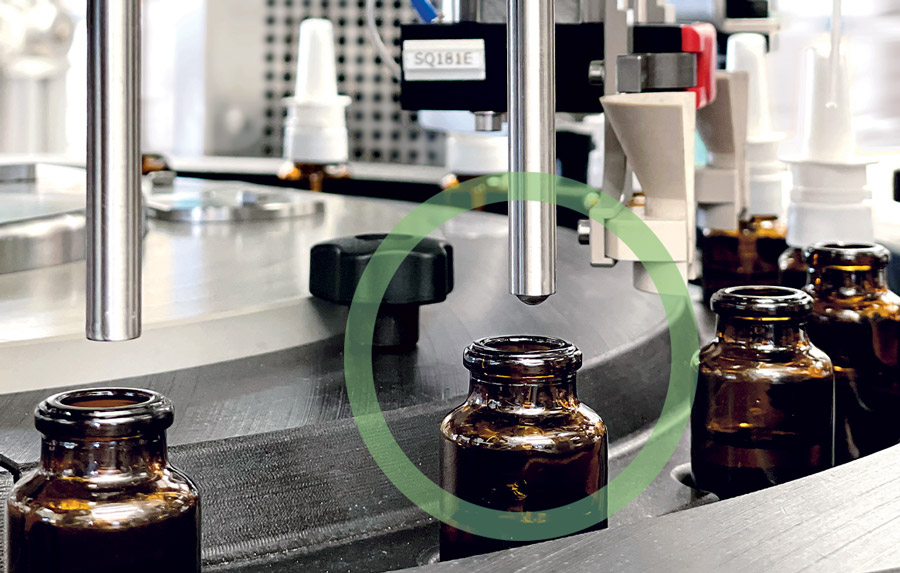
TECHNICAL DETAILS
This kind of technology guarantees many advantages:
↘ Cleanability. The circuit is only a pipe from pump to the filling head.
↘ Accuracy. The filling accuracy does not depend on the volume to be filled and can be improved by fine tuning of the setup of the machine.
↘ No limit of the filling capacity. The filling volume can be setup as required, even for filling many liters.
↘ Reduced changeover time. The time for changing the product is reduced to few minutes and it doesn’t require any adjustment, just put the filling volume in the HMI and the system start to fill.
↘ ELECTRONIC PUMP PLACING SYSTEM
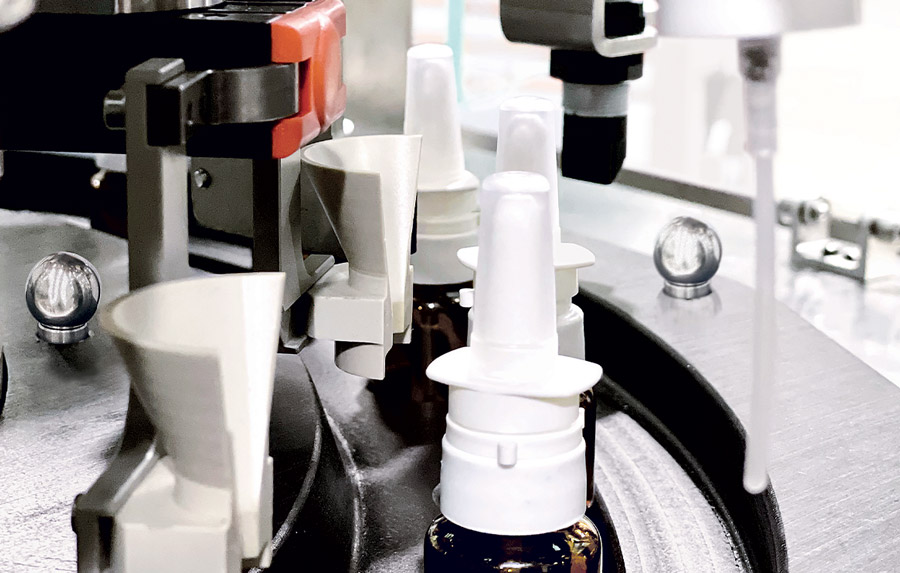
Advanced particle filtration
Q-A ir’s purifier combines powerful, high-efficiency pre-filtration with up to 301 square feet of HyperHEPA filtration media, tested and certified to effectively filter harmful ultrafine pollution particles down to 0.003 µ in size with an efficiency of 99.5%.
These tiny particles are 100 times smaller than what is filte- red with ordinary air filtration technology and up to 10 times smaller than a typical virus.